Inspection drone enable to fly autonomously in smoke stack
The drone specializes in smoke stack inspection. Proprietary control algorithm centers the drone inside the smoke stack enabling stable and continuous inspection inside smoke stack. Onboard LED illuminates the environment to help capture 60MP high-quality images for crack detection.
KEY FEATURE
Autonomous flight using LiDAR control and direction detection with lighting
In order to provide self-positioning in GPS-denied environments such as inside of a smoke stack, a LiDAR is being used. By taking advantage of LiDAR's unique ability to understand the shape of an object even in dark places, system creates point clouds of surroundings. The distance between the drone and the smoke stack wall is calculated by illuminating the smoke stack with LiDAR in the horizontal direction, and the drone is always controlled to stay in the center position. For orientation recognition, the lights on the smoke stack base are captured by a camera mounted on the drone. This allows the drone to recognize changes in its heading. These technologies enable the drone fly stably in the smoke stack of more than 100 meters high.
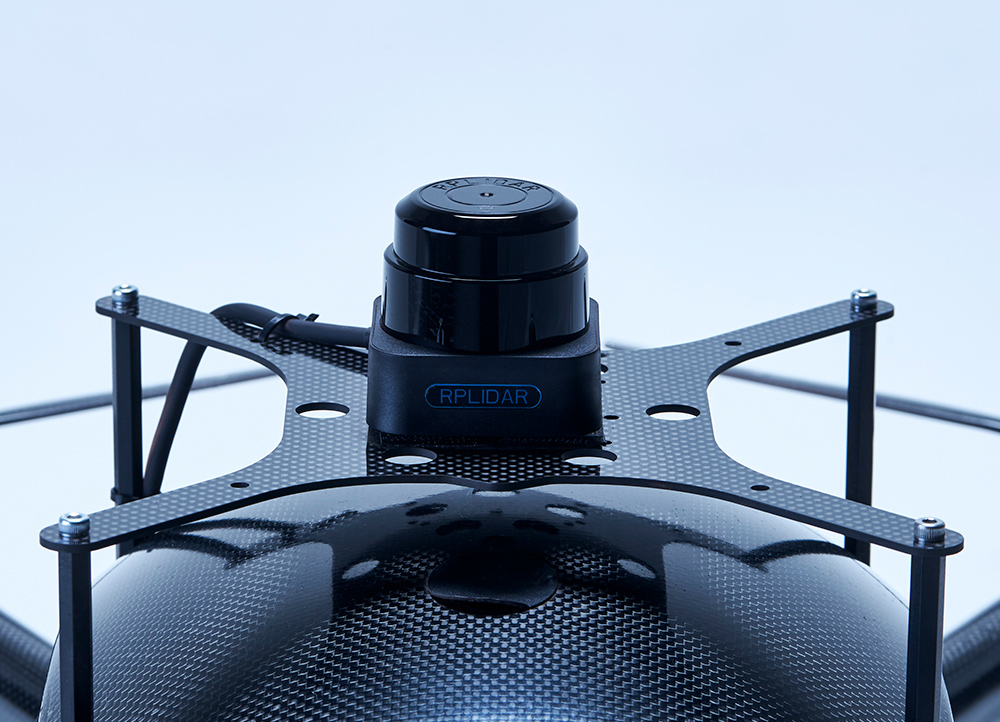
FEATURES
FEATURE 01
FLIGHT CONTROLLERACSL's proprietary control algorithmFlight controller is a critical component of the drone. ACSL has developed own flight controller based on proprietary advanced control algorithms.FEATURE 02
INSPECTION CAMERA0.5mm crack detectionA wide variety of cameras can be mounted as a payload. High-resolution cameras allows to detect up to 0.5mm degradation . (Example: SONY α7R4 70mm lens, shot from 5m distance)FEATURE 03
DRONE CONTROL WITH LiDARDrone control technology using LiDAR, which is good at confined spacesLiDAR technology makes it possible for drones to estimate their own position even in difficult situation for image recognition. (e.g. dark, no feature pattern.) Particularly in cylindrical structures such as tunnels and smoke stuck, where the cross-sectional structure is the same, is effective to control the position of the drone using LiDAR.FEATURE 01
FLIGHT CONTROLLERACSL's proprietary control algorithmFlight controller is a critical component of the drone. ACSL has developed own flight controller based on proprietary advanced control algorithms.FEATURE 02
INSPECTION CAMERA0.5mm crack detectionA wide variety of cameras can be mounted as a payload. High-resolution cameras allows to detect up to 0.5mm degradation . (Example: SONY α7R4 70mm lens, shot from 5m distance)FEATURE 03
DRONE CONTROL WITH LiDARDrone control technology using LiDAR, which is good at confined spacesLiDAR technology makes it possible for drones to estimate their own position even in difficult situation for image recognition. (e.g. dark, no feature pattern.) Particularly in cylindrical structures such as tunnels and smoke stuck, where the cross-sectional structure is the same, is effective to control the position of the drone using LiDAR.FEATURE 01
FLIGHT CONTROLLERACSL's proprietary control algorithmFlight controller is a critical component of the drone. ACSL has developed own flight controller based on proprietary advanced control algorithms.FEATURE 02
INSPECTION CAMERA0.5mm crack detectionA wide variety of cameras can be mounted as a payload. High-resolution cameras allows to detect up to 0.5mm degradation . (Example: SONY α7R4 70mm lens, shot from 5m distance)FEATURE 03
DRONE CONTROL WITH LiDARDrone control technology using LiDAR, which is good at confined spacesLiDAR technology makes it possible for drones to estimate their own position even in difficult situation for image recognition. (e.g. dark, no feature pattern.) Particularly in cylindrical structures such as tunnels and smoke stuck, where the cross-sectional structure is the same, is effective to control the position of the drone using LiDAR.
close visual inspection
under bridges and indoors
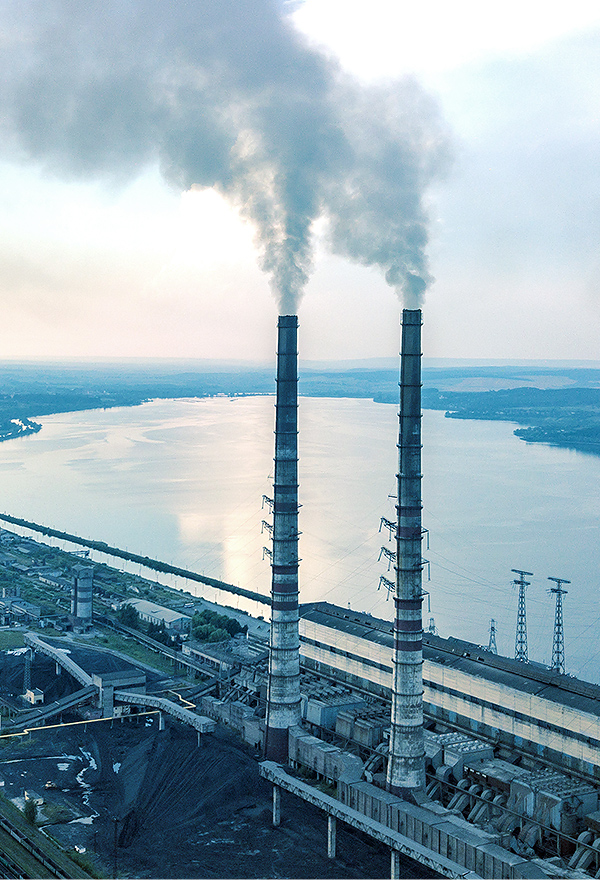
SCENE 01
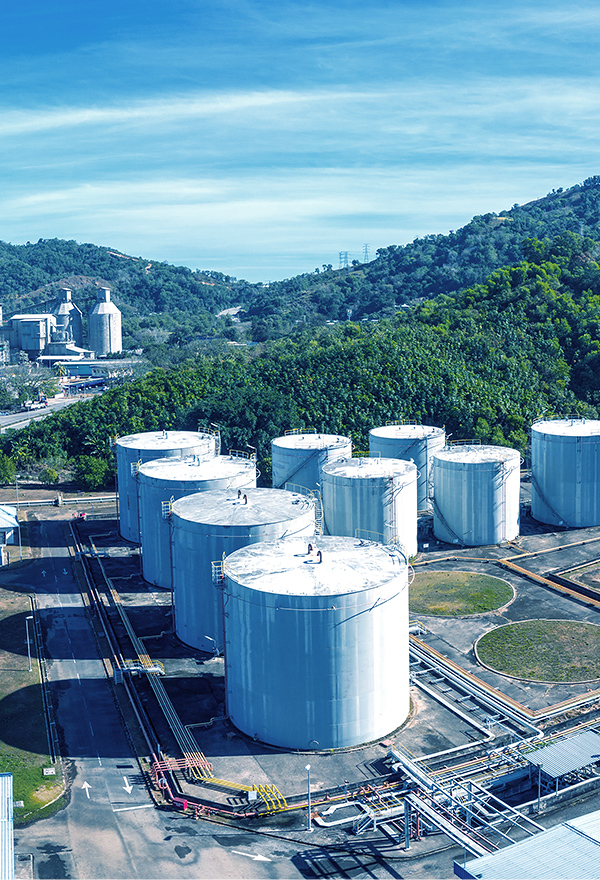
SCENE 02
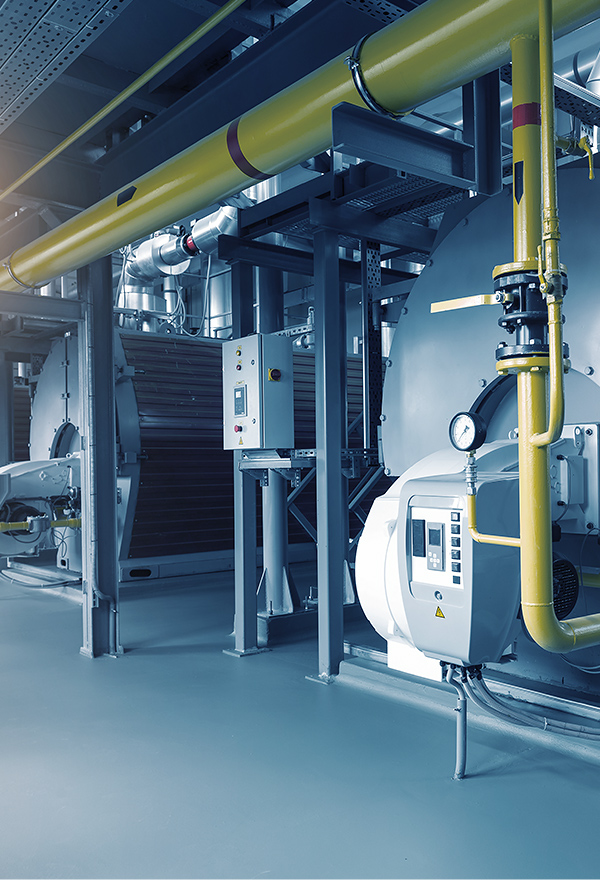
SCENE 03
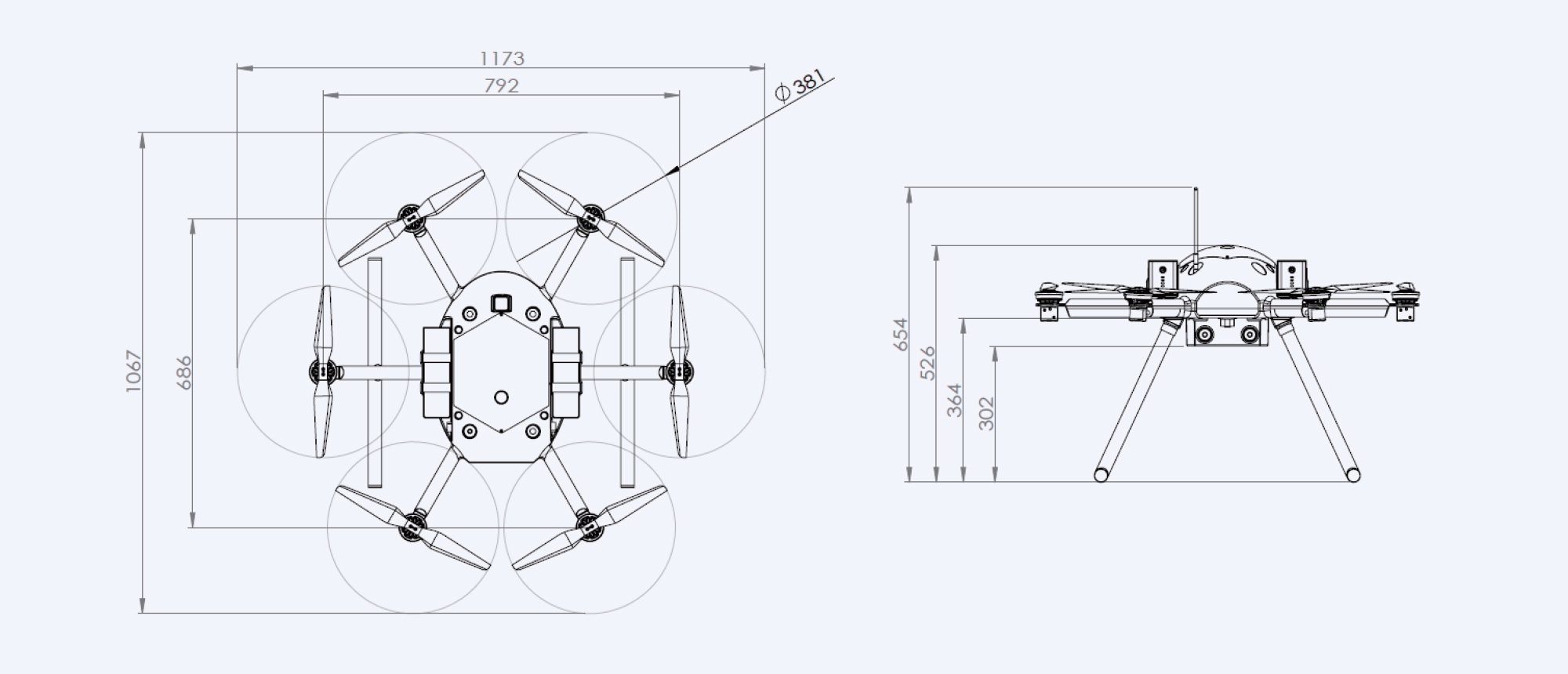
- STRUCTURE
-
- Width
- 1173 ㎜
- Height
- 654 ㎜
- Weight incl. 1 battery
- 7.07 ㎏
- COMMUNICATION SYSTEM
-
- Radio controller
- 2.4 GHz
- Telemetry link
- 920 MHz
- FLIGHT CONTROL SYSTEM
-
- Autopilot
- ACSL AP 3
- PERFORMANCE
-
- Flight speed(autonomous)
- Horizontal: 10 m/s Ascend: 3 m/s Descend: 2 m/s
- Altitude
- 150 m (Civil Aeronautics Law)
- Wind resistance
- 10m/s
- Maximum flight time
- 29 min (with no payload)
- Maximum pay load
- 2.75 ㎏
- BATTERY
-
- Capacity
- 12,000 mAh x2
- Normal Voltage
- 22.2 V
- Battery type
- LiPo 6s
- FUNCTION
-
- ■ Safety function
- Dustproof and waterproof: IP54
- Fail safe function in string wind
- Rout reverse return to home
- OPTION
-
- ■ 60M pix camera (SONY α7R4)
- ■ 5.7GHz video transmitter (license Not needed)
- ■ Propeller guard
The product specifications may change without prior notice.
The product specifications may change
without prior notice.
-
CASE 01
Plant facility regular monitoring using dronesDistance control for plant inspectionVisual SLAM technology can be applied to control drone at a constant distance from inspection target such as pipes and walls. This technology makes it easier to capture images at same angle, allowing inspector to compare the severity of the damage over time.
-
CASE 02
Visual SLAM for GPS-denied environmentVisual SLAM enabling indoor autonomous flightVisual SLAM computes drone position relative to the surrounding environment by extracting feature points and saving them as point cloud. This enables drone to conduct repetitive missions indoor, such as regular inspection of facility, warehouse stock counting, and tunnel inspection.
-
CASE 01
Plant facility regular monitoring using dronesDistance control for plant inspectionVisual SLAM technology can be applied to control drone at a constant distance from inspection target such as pipes and walls. This technology makes it easier to capture images at same angle, allowing inspector to compare the severity of the damage over time.
-
CASE 02
Visual SLAM for GPS-denied environmentVisual SLAM enabling indoor autonomous flightVisual SLAM computes drone position relative to the surrounding environment by extracting feature points and saving them as point cloud. This enables drone to conduct repetitive missions indoor, such as regular inspection of facility, warehouse stock counting, and tunnel inspection.
-
CASE 01
Plant facility regular monitoring using dronesDistance control for plant inspectionVisual SLAM technology can be applied to control drone at a constant distance from inspection target such as pipes and walls. This technology makes it easier to capture images at same angle, allowing inspector to compare the severity of the damage over time.
-
CASE 02
Visual SLAM for GPS-denied environmentVisual SLAM enabling indoor autonomous flightVisual SLAM computes drone position relative to the surrounding environment by extracting feature points and saving them as point cloud. This enables drone to conduct repetitive missions indoor, such as regular inspection of facility, warehouse stock counting, and tunnel inspection.