Inspection drone with automatic still image upload and AI-based degradation detection
ACSL has automated pipeline inspection process. The end-to-end system autonomously captures images, uploads the images to the cloud, analyses with AI, and develops inspection reports. On-board 20 MP inspection camera collects high-quality images from hard-to-reach places.
KEY FEATURE
Automatic still image upload and AI-based degradation detection
Previously, drones were just used to collect images. In this system, drone collects geo-tagged images and automatically uploads them to cloud storage upon landing. Stored images are then processed using damage recognition AI. This end-to-end solution enables to reduces time and cost of inspection workflow.
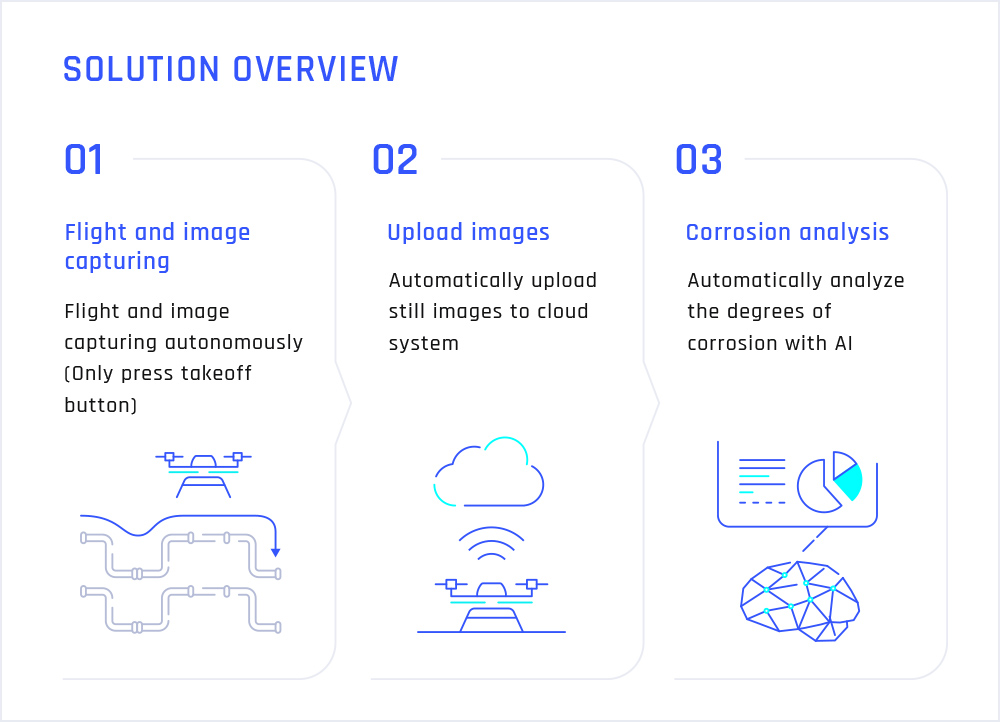
FEATURES
FEATURE 01
AI-BASED IMAGE ANALYSIS AND DAMAGE LEVEL JUDGEMENTEnables AI evaluation on the cloud systemAI based image analysis software that runs on the cloud provided by Accenture, Inc. enables to judge the damages automatically. (e.g. pipe corrosion, oil tank leaks, etc.) This system provide a complete range of services, from flight photography to image analysis and inspection reports.FEATURE 02
AUTOMATICALLY STILL IMAGE UPLOADAutomatic upload of captured still images to the cloudThe system automatically upload the images captured by the drone to the cloud after flight. Automatic upload function eliminates to export the still image manually. That allows you to work more efficiently.FEATURE 01
AI-BASED IMAGE ANALYSIS AND DAMAGE LEVEL JUDGEMENTEnables AI evaluation on the cloud systemAI based image analysis software that runs on the cloud provided by Accenture, Inc. enables to judge the damages automatically. (e.g. pipe corrosion, oil tank leaks, etc.) This system provide a complete range of services, from flight photography to image analysis and inspection reports.FEATURE 02
AUTOMATICALLY STILL IMAGE UPLOADAutomatic upload of captured still images to the cloudThe system automatically upload the images captured by the drone to the cloud after flight. Automatic upload function eliminates to export the still image manually. That allows you to work more efficiently.FEATURE 01
AI-BASED IMAGE ANALYSIS AND DAMAGE LEVEL JUDGEMENTEnables AI evaluation on the cloud systemAI based image analysis software that runs on the cloud provided by Accenture, Inc. enables to judge the damages automatically. (e.g. pipe corrosion, oil tank leaks, etc.) This system provide a complete range of services, from flight photography to image analysis and inspection reports.FEATURE 02
AUTOMATICALLY STILL IMAGE UPLOADAutomatic upload of captured still images to the cloudThe system automatically upload the images captured by the drone to the cloud after flight. Automatic upload function eliminates to export the still image manually. That allows you to work more efficiently.
close visual inspection
under bridges and indoors
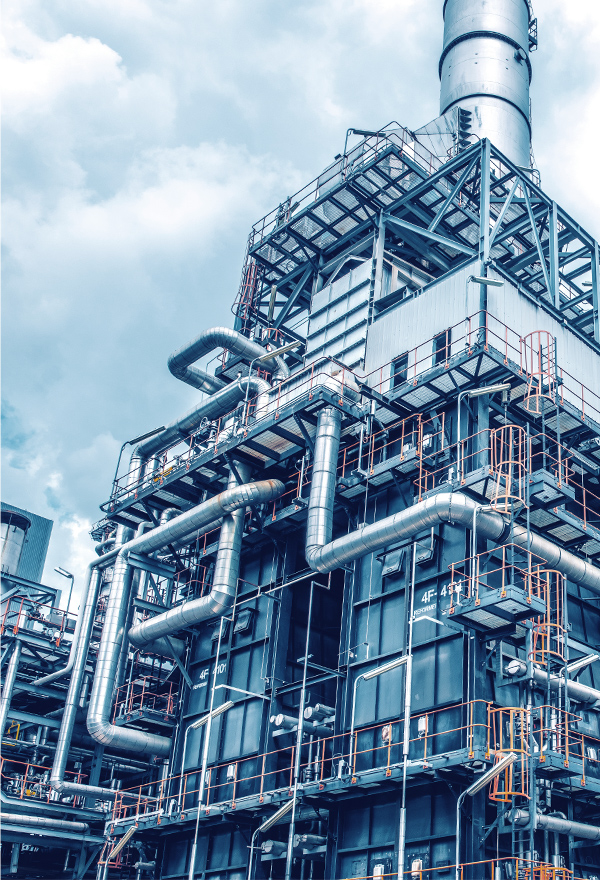
SCENE 01
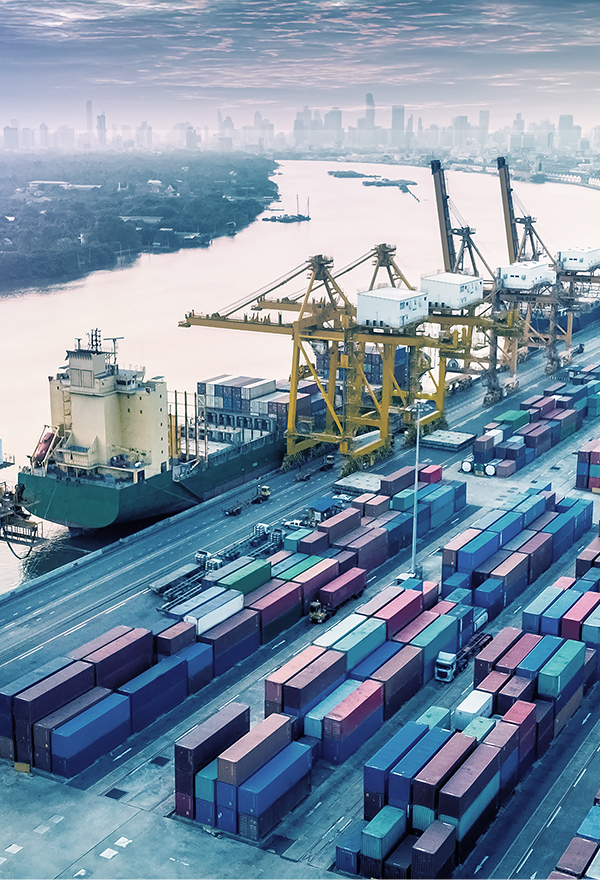
SCENE 02
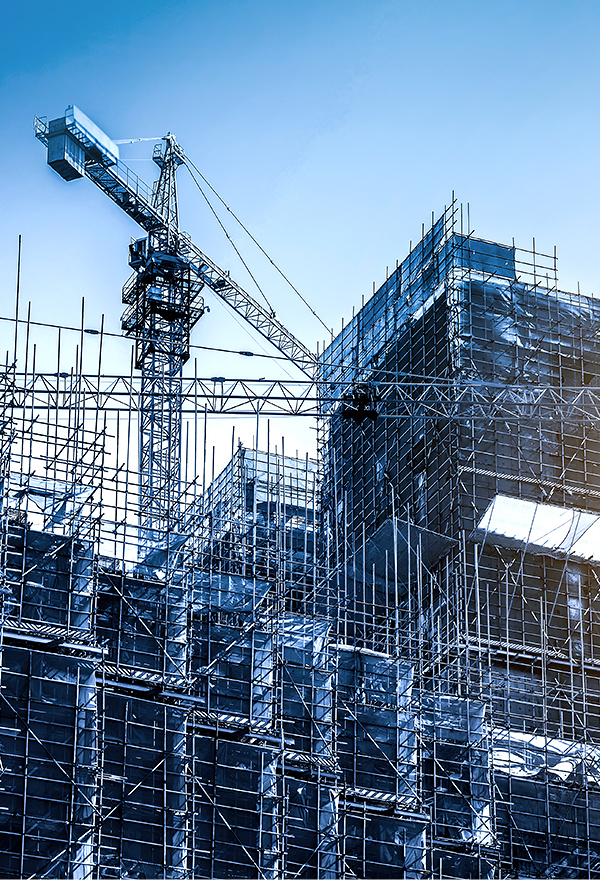
SCENE 03
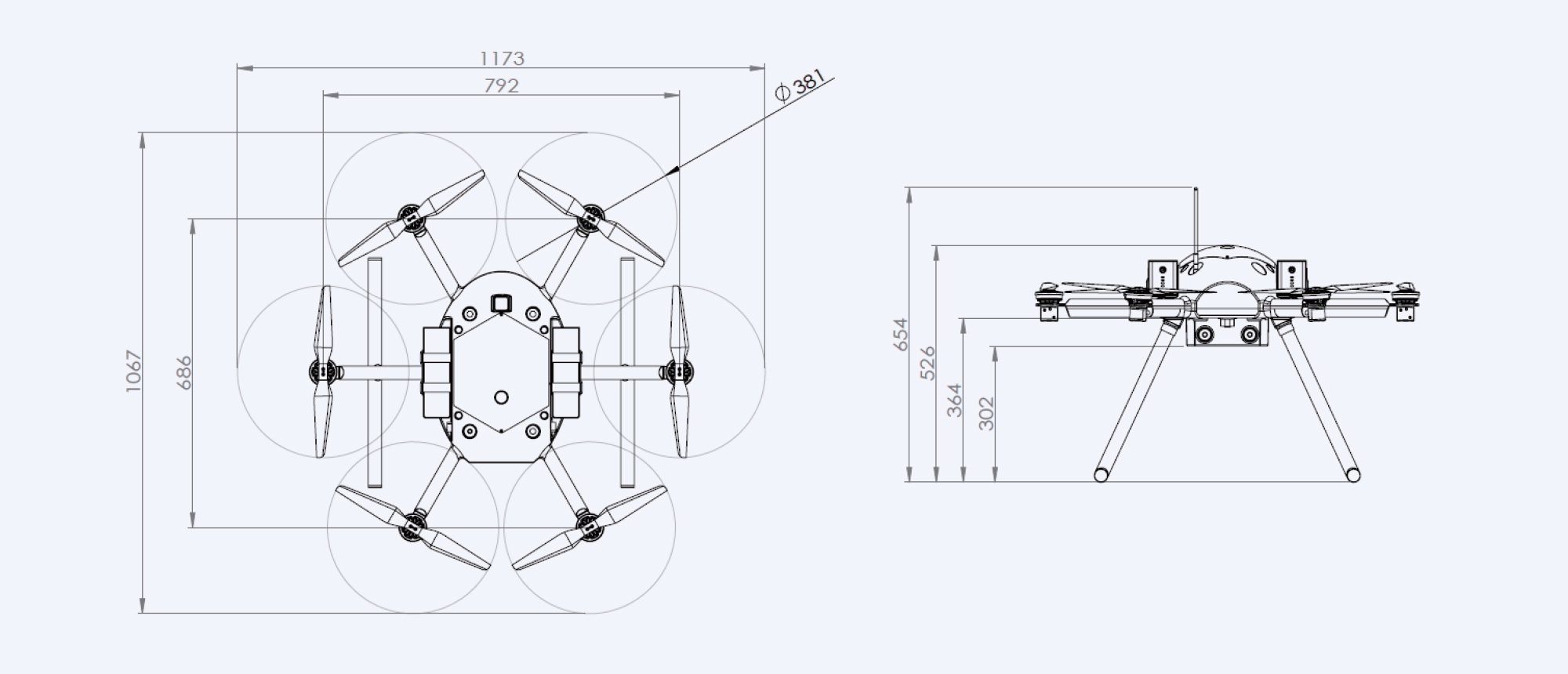
- STRUCTURE
-
- Width
- 1173 ㎜
- Height
- 654 ㎜
- Weight incl. 1 battery
- 7.07 ㎏
- COMMUNICATION SYSTEM
-
- Radio controller
- 2.4 GHz
- Telemetry link
- 920 MHz
- FLIGHT CONTROL SYSTEM
-
- Autopilot
- ACSL AP 3
- PERFORMANCE
-
- Flight speed(autonomous)
- Horizontal: 10 m/s Ascend: 3 m/s Descend: 2 m/s
- Altitude
- 150 m (Civil Aeronautics Law)
- Wind resistance
- 10m/s
- Maximum flight time
- 29 min (with no payload)
- Maximum pay load
- 2.75 ㎏
- BATTERY
-
- Capacity
- 12,000 mAh x2
- Normal Voltage
- 22.2 V
- Battery type
- LiPo 6s
- FUNCTION
-
- ■ Safety function
- Dustproof and waterproof: IP54
- Fail safe function in string wind
- Rout reverse return to home
- OPTION
-
- ■ Rust detection AI
- ■ 20M pix camera (SONY R10C)
- ■ x30 zoom camera (SONY QX30U)
- ■ 5.7GHz video transmitter (license Not needed)
- ■ Wi-Fi communication for photo uploader
The product specifications may change without prior notice.
The product specifications may change
without prior notice.
-
CASE 01
Plant facility regular monitoring using dronesDistance control for plant inspectionVisual SLAM technology can be applied to control drone at a constant distance from inspection target such as pipes and walls. This technology makes it easier to capture images at same angle, allowing inspector to compare the severity of the damage over time.
-
CASE 02
Visual SLAM for GPS-denied environmentVisual SLAM enabling indoor autonomous flightVisual SLAM computes drone position relative to the surrounding environment by extracting feature points and saving them as point cloud. This enables drone to conduct repetitive missions indoor, such as regular inspection of facility, warehouse stock counting, and tunnel inspection.
-
CASE 01
Plant facility regular monitoring using dronesDistance control for plant inspectionVisual SLAM technology can be applied to control drone at a constant distance from inspection target such as pipes and walls. This technology makes it easier to capture images at same angle, allowing inspector to compare the severity of the damage over time.
-
CASE 02
Visual SLAM for GPS-denied environmentVisual SLAM enabling indoor autonomous flightVisual SLAM computes drone position relative to the surrounding environment by extracting feature points and saving them as point cloud. This enables drone to conduct repetitive missions indoor, such as regular inspection of facility, warehouse stock counting, and tunnel inspection.
-
CASE 01
Plant facility regular monitoring using dronesDistance control for plant inspectionVisual SLAM technology can be applied to control drone at a constant distance from inspection target such as pipes and walls. This technology makes it easier to capture images at same angle, allowing inspector to compare the severity of the damage over time.
-
CASE 02
Visual SLAM for GPS-denied environmentVisual SLAM enabling indoor autonomous flightVisual SLAM computes drone position relative to the surrounding environment by extracting feature points and saving them as point cloud. This enables drone to conduct repetitive missions indoor, such as regular inspection of facility, warehouse stock counting, and tunnel inspection.