Inspection drone enable to fly autonomously in GPS denied
Drones can be utilized for floor inspection inside warehouses, distribution centers, and large retail stores. Utilizing GPS-denied navigation algorithms, this drone operates on pre-determined flight route to capture high-resolution images of floor from certain altitude, making inspection work to be faster and more efficient.
KEY FEATURE
Flight control technology integrate with multiple sensors
In order to achieve autonomous flight inside warehouses and distribution centers, ACSL utilizes LiDAR and Time-of-flight (ToF) sensor information fused together to allow precision localization. Moreover, these sensors measure distances from surrounding environment and enable drone to keep safe distance from obstacles around.
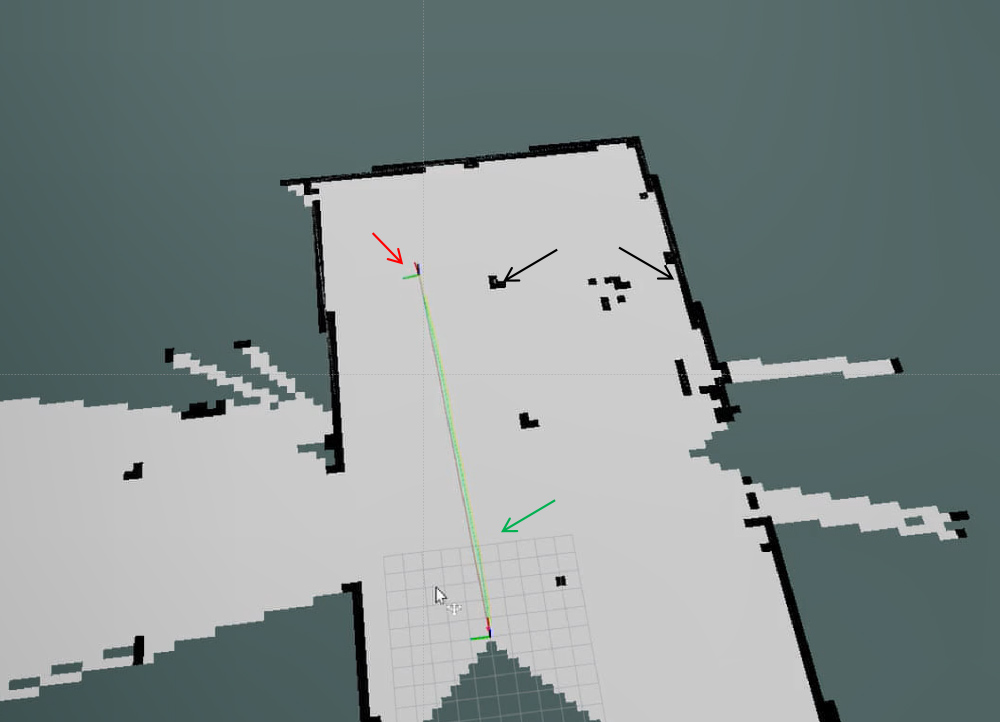
FEATURES
FEATURE 01
INSPECTION CAMERA0.5mm crack detectionA wide variety of cameras can be mounted as a payload. High-resolution cameras allows to detect up to 0.5mm degradation . (Example: SONY α7R4 70mm lens, shot from 5m distance)FEATURE 02
FLIGHT CONTROLLERACSL's proprietary control algorithmFlight controller is a critical component of the drone. ACSL has developed own flight controller based on proprietary advanced control algorithms.FEATURE 03
PF-STATIONFully remote control in autonomous flightFor safety drone operation, the control information integrated into one. Various drone telemetry information is monitored in real-time and managed. Check the battery level, data communication status, current position and flight route, etc. at a glance, and the system gives warning if abnormal situation happens.FEATURE 01
INSPECTION CAMERA0.5mm crack detectionA wide variety of cameras can be mounted as a payload. High-resolution cameras allows to detect up to 0.5mm degradation . (Example: SONY α7R4 70mm lens, shot from 5m distance)FEATURE 02
FLIGHT CONTROLLERACSL's proprietary control algorithmFlight controller is a critical component of the drone. ACSL has developed own flight controller based on proprietary advanced control algorithms.FEATURE 03
PF-STATIONFully remote control in autonomous flightFor safety drone operation, the control information integrated into one. Various drone telemetry information is monitored in real-time and managed. Check the battery level, data communication status, current position and flight route, etc. at a glance, and the system gives warning if abnormal situation happens.FEATURE 01
INSPECTION CAMERA0.5mm crack detectionA wide variety of cameras can be mounted as a payload. High-resolution cameras allows to detect up to 0.5mm degradation . (Example: SONY α7R4 70mm lens, shot from 5m distance)FEATURE 02
FLIGHT CONTROLLERACSL's proprietary control algorithmFlight controller is a critical component of the drone. ACSL has developed own flight controller based on proprietary advanced control algorithms.FEATURE 03
PF-STATIONFully remote control in autonomous flightFor safety drone operation, the control information integrated into one. Various drone telemetry information is monitored in real-time and managed. Check the battery level, data communication status, current position and flight route, etc. at a glance, and the system gives warning if abnormal situation happens.
location of goods inside
warehouses
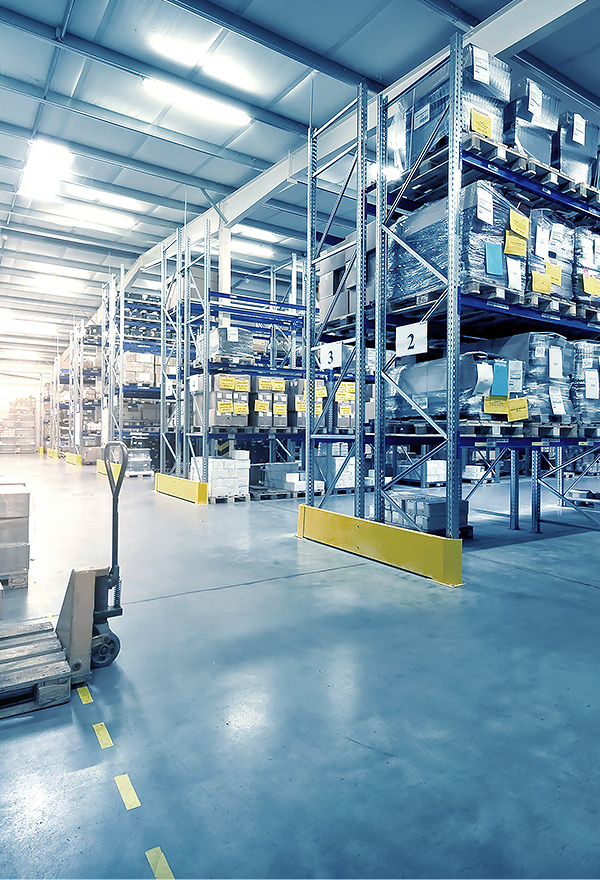
SCENE 01
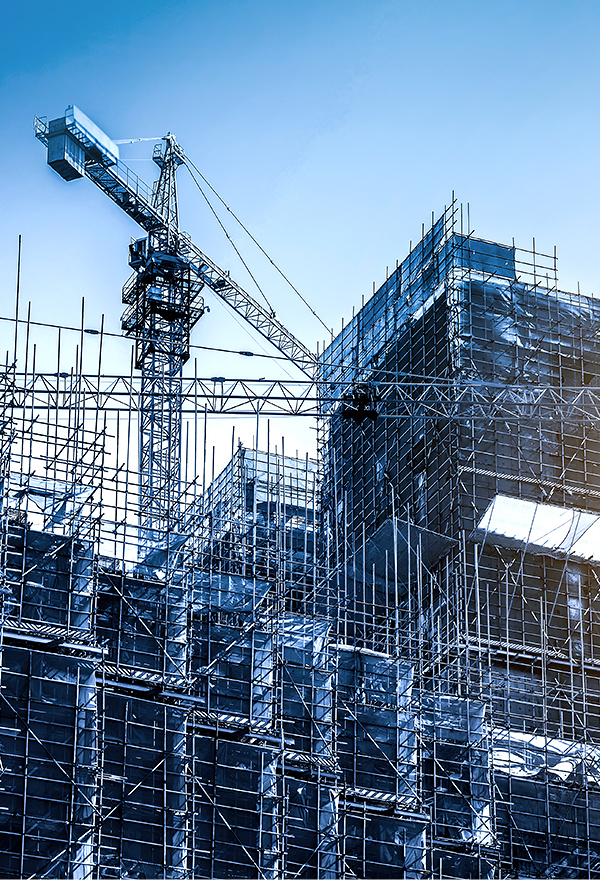
SCENE 02
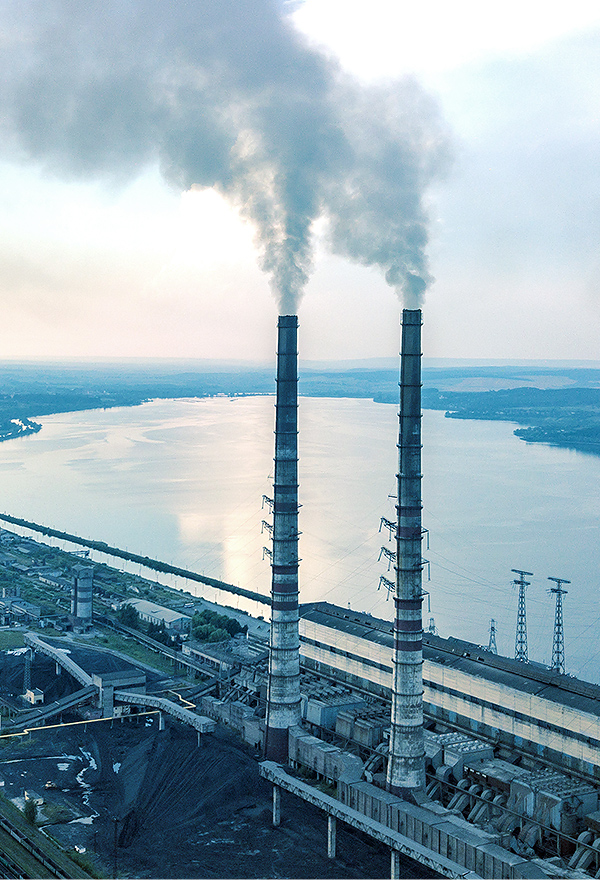
SCENE 03
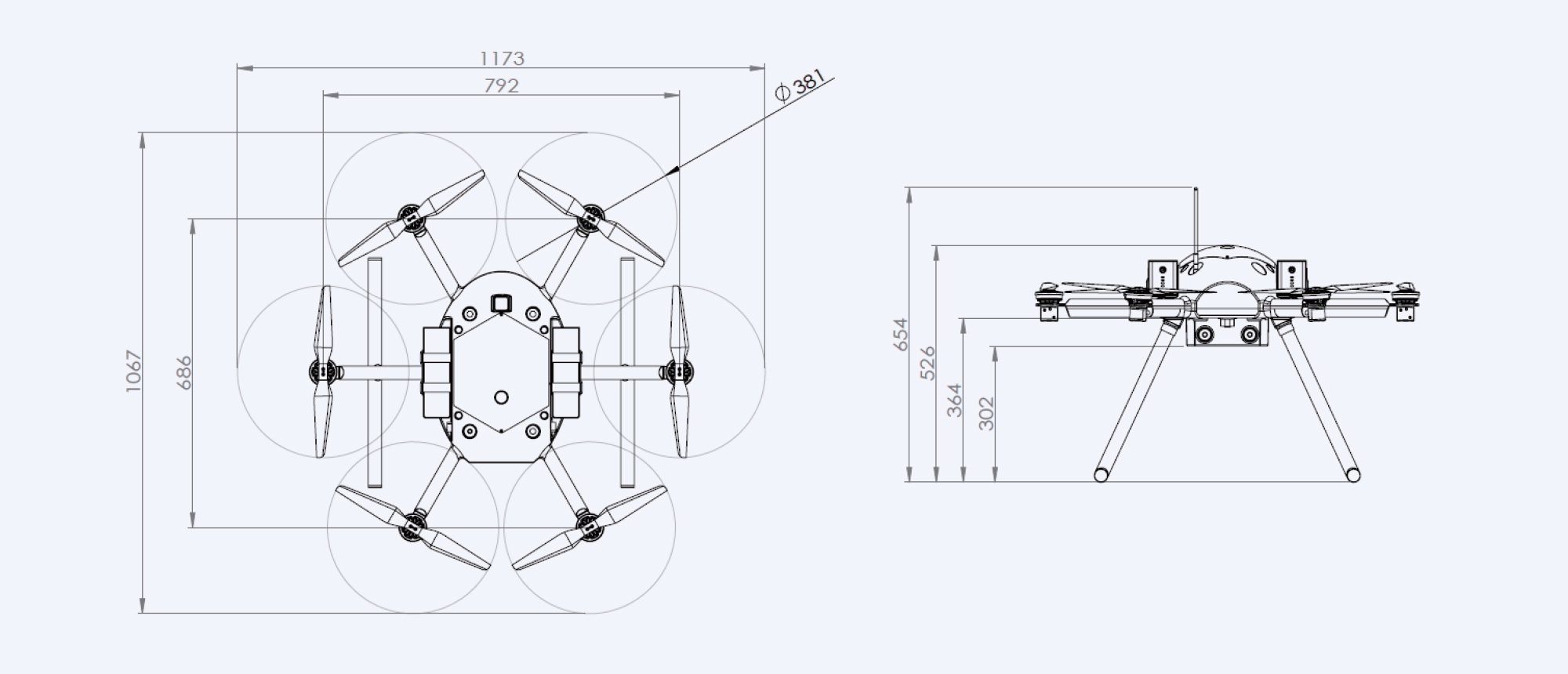
- STRUCTURE
-
- Width
- 1173 ㎜
- Height
- 654 ㎜
- Weight incl. 1 battery
- 7.07 ㎏
- COMMUNICATION SYSTEM
-
- Radio controller
- 2.4 GHz
- Telemetry link
- 920 MHz
- FLIGHT CONTROL SYSTEM
-
- Autopilot
- ACSL AP 3
- PERFORMANCE
-
- Flight speed(autonomous)
- Horizontal: 10 m/s Ascend: 3 m/s Descend: 2 m/s
- Altitude
- 150 m (Civil Aeronautics Law)
- Wind resistance
- 10m/s
- Maximum flight time
- 29 min (with no payload)
- Maximum pay load
- 2.75 ㎏
- BATTERY
-
- Capacity
- 12,000 mAh x2
- Normal Voltage
- 22.2 V
- Battery type
- LiPo 6s
- FUNCTION
-
- ■ Safety function
- Dustproof and waterproof: IP54
- Fail safe function in string wind
- Rout reverse return to home
- OPTION
-
- ■ 20M pix camera (SONY R10C)
- ■ Propeller guard
- ■ 5.7GHz video transmitter (license Not needed)
The product specifications may change without prior notice.
The product specifications may change
without prior notice.
-
CASE 01
Nishimatsu Construction, Auto-crack detection for concrete floorAutomating concrete floor crack detection using dronesNishimatsu Construction and ACSL developed a system to automatically detect cracks in concrete floors. This system consists of autonomous drone that operate in indoor environment, and concrete crack detection algorithm. Compared to conventional method, it is expected to improve the quality of crack detection, and to reduce the cost for conducting the inspection.
-
CASE 02
Visual SLAM for GPS-denied environmentVisual SLAM enabling indoor autonomous flightVisual SLAM computes drone position relative to the surrounding environment by extracting feature points and saving them as point cloud. This enables drone to conduct repetitive missions indoor, such as regular inspection of facility, warehouse stock counting, and tunnel inspection.
-
CASE 01
Nishimatsu Construction, Auto-crack detection for concrete floorAutomating concrete floor crack detection using dronesNishimatsu Construction and ACSL developed a system to automatically detect cracks in concrete floors. This system consists of autonomous drone that operate in indoor environment, and concrete crack detection algorithm. Compared to conventional method, it is expected to improve the quality of crack detection, and to reduce the cost for conducting the inspection.
-
CASE 02
Visual SLAM for GPS-denied environmentVisual SLAM enabling indoor autonomous flightVisual SLAM computes drone position relative to the surrounding environment by extracting feature points and saving them as point cloud. This enables drone to conduct repetitive missions indoor, such as regular inspection of facility, warehouse stock counting, and tunnel inspection.
-
CASE 01
Nishimatsu Construction, Auto-crack detection for concrete floorAutomating concrete floor crack detection using dronesNishimatsu Construction and ACSL developed a system to automatically detect cracks in concrete floors. This system consists of autonomous drone that operate in indoor environment, and concrete crack detection algorithm. Compared to conventional method, it is expected to improve the quality of crack detection, and to reduce the cost for conducting the inspection.
-
CASE 02
Visual SLAM for GPS-denied environmentVisual SLAM enabling indoor autonomous flightVisual SLAM computes drone position relative to the surrounding environment by extracting feature points and saving them as point cloud. This enables drone to conduct repetitive missions indoor, such as regular inspection of facility, warehouse stock counting, and tunnel inspection.